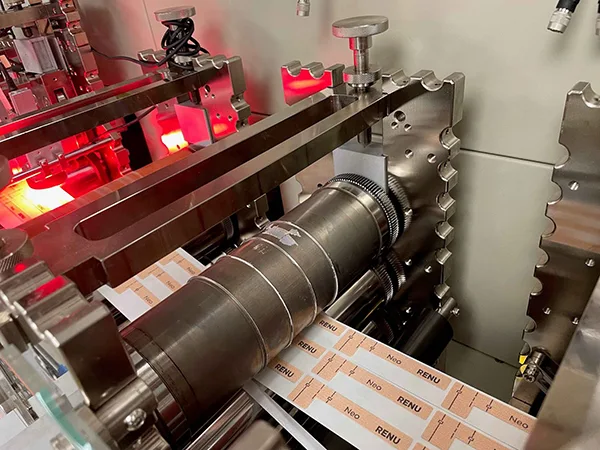
As a person I have great respect for doctors, they save lives and even to do that they dedicate half of their lives to studies. When they finally become a doctor, they cure and treat people by doing something only a higher entity can. But do you know the tools they use are created with great precision? And what changes have come in this field?
Gale Sayers once said, “I know with my knee injury, I didn’t have the type of medical technology we have today. If I could’ve had what we had now, I probably could’ve been back out in three months. I didn’t have that”. This statement shows that yes, in comparison to back then we have advanced so much. Just so you know, die-cutting is a process in which specialized machines are used to create different things. It could be any tool, toy, or pretty much anything else.
In this article, I will talk about tech-driven innovations in medical die-cutting for enhanced precision. This write-up will follow all the advantages we are getting with medical die-cutting technology, so be ready. Also, learn about Hospitals Need High-Quality Medical Weighing Scales by reading this article.
Digital Advancements for Greater Accuracy
Different tools and pieces of software have been introduced in the making of medical devices, which has resulted in greater accuracy. One of the most commonly used pieces of software is CAD or Computer-aided design. This program enables you to create, modify, or analyze any 2D-3D designs and models.
Laser cutting technology has also been introduced, which makes things a lot easier and smoothens the process along with making perfect products. There is no denying that cutting-edge technology was a step forward toward digital advancement, and the results are looking great so far.
Advanced Materials and Customization
Since the introduction of die cutting, new advanced materials have been used for creating medical devices and tools. Why? Because this technology has made shearing, cutting, and forming easier. So now we are not limited to materials, as we can effectively use new ones.
For example, medical-grade silicone, and biocompatible polymers are being used more because customizing them has become easier. Since every medically used tool has to meet a specific standard, die-cutting does that without any struggle. Biocompatibility, flexibility, and durability all are taken care of.
Cost Efficiency Through Tech-Driven Solutions
There are different types of dye-cutting embedded machines specially created for medical tools, so they are very accurate. They don’t cut off excess material, instead work with limited material, cutting down on wastage and maintaining cost efficiency.
For example, if you take a look at PolarSeal they use this technology and have reduced their cost by decreasing the wastage of material, but they didn’t compromise the quality of the final product.
If you are wondering just how big the die cutting machine market is than take a look at the graph below and it would clear your question.
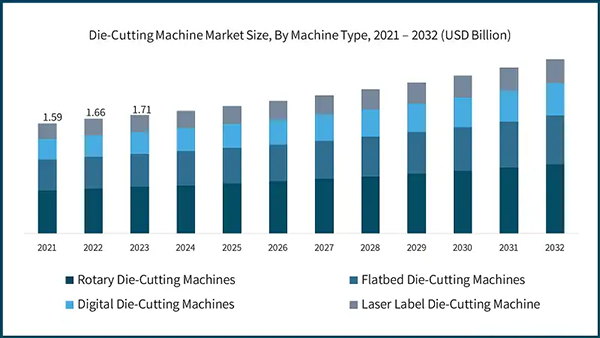
The Role of Automation and Robotics
We all know that robots and automation have started replacing manual work, making this easier and resulting in better accuracy. Machines and computerized processes play a significant role in die cutting, which is why it has enhanced precision.
Automation ensures that the work is being done constantly where products are produced continuously. On the other hand, robots keep all the relative tasks in check, like handling and putting things together. As they work in great sync, it maintains the workflow, production, and accuracy.
Enhanced Quality Control Through Smart Technologies
I think smart technologies like real-time data management and analysis are essential in all fields. This same thing applies to die cutting because machine learning and data analysis are two of the important components of production. Without them, a lot of things can go wrong.
For starters, without these tools, monitoring won’t be possible. So even if there are imperfections and the product is not up to the standards, you won’t be able to detect it yourself. The monitoring system plays a crucial role in quality control, and it allows manufacturers to maintain product integrity.
DID YOU KNOW?
The first ever die-cutting machine was invented in 1977 called Ellison LetterMachine!
Future Prospects and Innovations
It’s true that with each year we are met with new innovations, and they only help us improve more. Die cutting has turned out to be a revolution, not only is it cost-efficient it gives us quality and is a lot faster than traditional methods. As for the future, we are definitely going to see more changes in die cutting and those changes will make it even better than it already is.
Even though these technologies are benefiting our lives we still don’t have to get totally dependent on them, it’s not the machine that runs a human, it’s a human that runs a machine, always remember that.